tmax-Integraldämmungen besitzen einen Mantel aus Edelstahlfolien oder Feinblech, der perfekt an die Konturen der zu dämmenden Objekte angepasst ist. Zusätzlich eingeprägte Strukturen erhöhen die Steifigkeit und ermöglichen so minimale Wandstärken der eingesetzten Materialien. Beides wird durch den Einsatz modernster Präge- und Formwerkzeuge möglich. Hier geben wir Ihnen einen Einblick in die über 25-jährige Entwicklungsgeschichte der Presswerkzeuge bei der tmax.
Werkzeugbau früher und heute
Mit der Forderung nach passgenauen und reproduzierbaren Folienschalen mussten in den 90er-Jahren neue Wege in der Fertigung bei tmax gegangen werden, denn die vorhandenen Werkzeuge und Methoden des Werkzeugbau – Kantbank, Rollbiegemaschine, Schablonen usw. – stießen an ihre Grenzen.
Man begann mit einer – aus heutiger Sicht eher schwachen – 30-Tonnen-Presse und mit Enthusiasmus die ersten Presswerkzeuge dafür selbst herzustellen. Viel handwerkliches Geschick war erforderlich, um ohne Maschinen ein Negativmodell des Werkzeugs zu erstellen und dieses dann in einem Holzkasten mit Gießharz abzuformen. Einige Werkzeuge sind heute, nach 20 Jahren, noch immer im Einsatz!
Neue Fertigungsverfahren
Mit Beginn der 2000er-Jahre wurden die Presswerkzeuge aus Gießharz zunehmend von CNC-gefrästen Presswerkzeugen verdrängt. Da diese CAD-Daten basiert gefertigt wurden, waren sie nicht nur präziser, sondern auch sehr gut reproduzierbar und der Aufwand für ihre Herstellung bedeutend geringer. Für das Fräsen der Presswerkzeuge wurden anfangs Aufträge an Werkzeug- und Formenbauer aus der Region vergeben.
Zu dieser Zeit wurde auch Werkzeugverschleiß erstmals zum Thema, weshalb zunehmend Presswerkzeuge aus widerstandsfähigem Kunststoff gefräst und mit Verschleißplatten ausgestattet wurden. Bei der Werkstoffauswahl vertraute man auf die Empfehlungen externer Werkzeugkonstrukteure.
Presswerkzeuge im Wandel
Ab 2010 führte der Einstieg von tmax in den Automotive-Bereich und immer strengere Abgasrichtlinien zu vielen neuen Projekten und einer hohen Nachfrage nach Integraldämmungen. Mit dem Anspruch, schnell auf Kundenwünsche reagieren zu können, wurde 2011 die Abteilung Werkzeugbau gegründet und eine erste, dann 2012 eine zweite CNC-Fräsmaschine angeschafft. Die Fertigung der Presswerkzeuge erfolgte in den Jahren 2011 bis 2014 sowohl intern als auch extern. Die Anzahl der Presswerkzeuge stieg schnell auf über 1000 Stück an.
Die Zeit der Stahlwerkzeuge
Ab 2016 erhöhten sich die Stückzahlen der Integraldämmung ein weiteres Mal enorm. Schnell war klar – um dem Werkzeugverschleiß entgegenzuwirken und von der ersten bis zur letzten Folienschale kompromisslos gute Qualität zu fertigen, müssen alle Presswerkzeuge für die Serie aus Stahl gefertigt werden. Für ihre Herstellung wurde ab 2018 eine weitere CNC-Fräsmaschine angeschafft.
In den letzten Jahren hat die tmax viel in den Ausbau der substrativen und additiven Verfahren des eigenen Werkzeugbaus investiert. So fertigen wir heute mit drei Fräsmaschinen präzise und genaue Stempel und Matrizen aus hochwertigen Werkzeugstahl-Blöcken für die Presswerkzeuge. Zudem können in zwei 3D-Druckern Masken für die Laservorrichtungen aus Kunststoff hergestellt werden. Da sich die Formen unserer Isolierteile an der Bauteilform von unseren Kunden orientieren, setzen wir auf hochdynamische Fräsmaschinen von DMG MORI und Steuerungen von Heidenhain.
Werkzeuge aus Kunststoff werden nur noch für Prototypen verwendet.
Heute stützt sich die tmax auf seinen eigenen Werkzeugbau, nur in sehr seltenen Fällen wird auf langjährige Partner zurückgegriffen.
Ein Serienwerkzeug bei tmax hat mit den Werkzeugen vor 25 Jahren nicht mehr viel gemeinsam. Aus hochwertigem Werkzeugstahl wird auf hochmodernen Fräsmaschinen die Form gefräst, spezielle Härteverfahren und Beschichtungen/Polituren erhöhen die Standzeit der Werkzeuge auf mehrere Millionen Stück bei nahezu gleichbleibender Qualität von der ersten bis zur letzten Schale. „Das Presswerkzeug heute ist massiver und wartungsfreundlicher. Fakt ist, die Entwicklung geht weiter und es bleibt spannend“, sagt der Leiter des Werkzeugbaus Mathias Lang.
Integrierte automatische Sprühsysteme: Es gibt derzeit Versuche, ein Öl-Sprühsystem in das Werkzeug einzubringen. Ziel ist, Risse bei sehr dünnen Folien und komplizierten Formen zu vermeiden. Die Folie wird vor dem Pressen mit Öl besprüht, um das Gleiten der Folie am Werkzeug zu verbessern.
Mikrofräsen: Die Optimierung des Fräsverfahrens und die Zusammenarbeit mit unserem CAM-Software-Lieferanten ermöglichte es, dieses neue Verfahren einzuführen. Mit dem Mikrofräsen können sehr filigrane Konturen, Firmenlogos, Symbole, Warnzeichen usw. in das Werkzeug eingebracht werden.
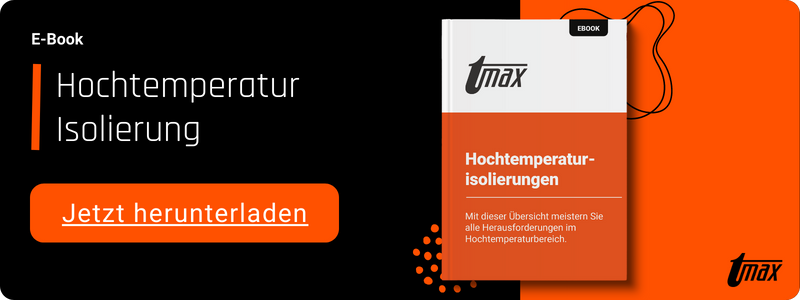